I cleaned old glue off of the motor axle and re-glued it after my last post. Yesterday I mounted the motor/lead screw and spindle to the machine.
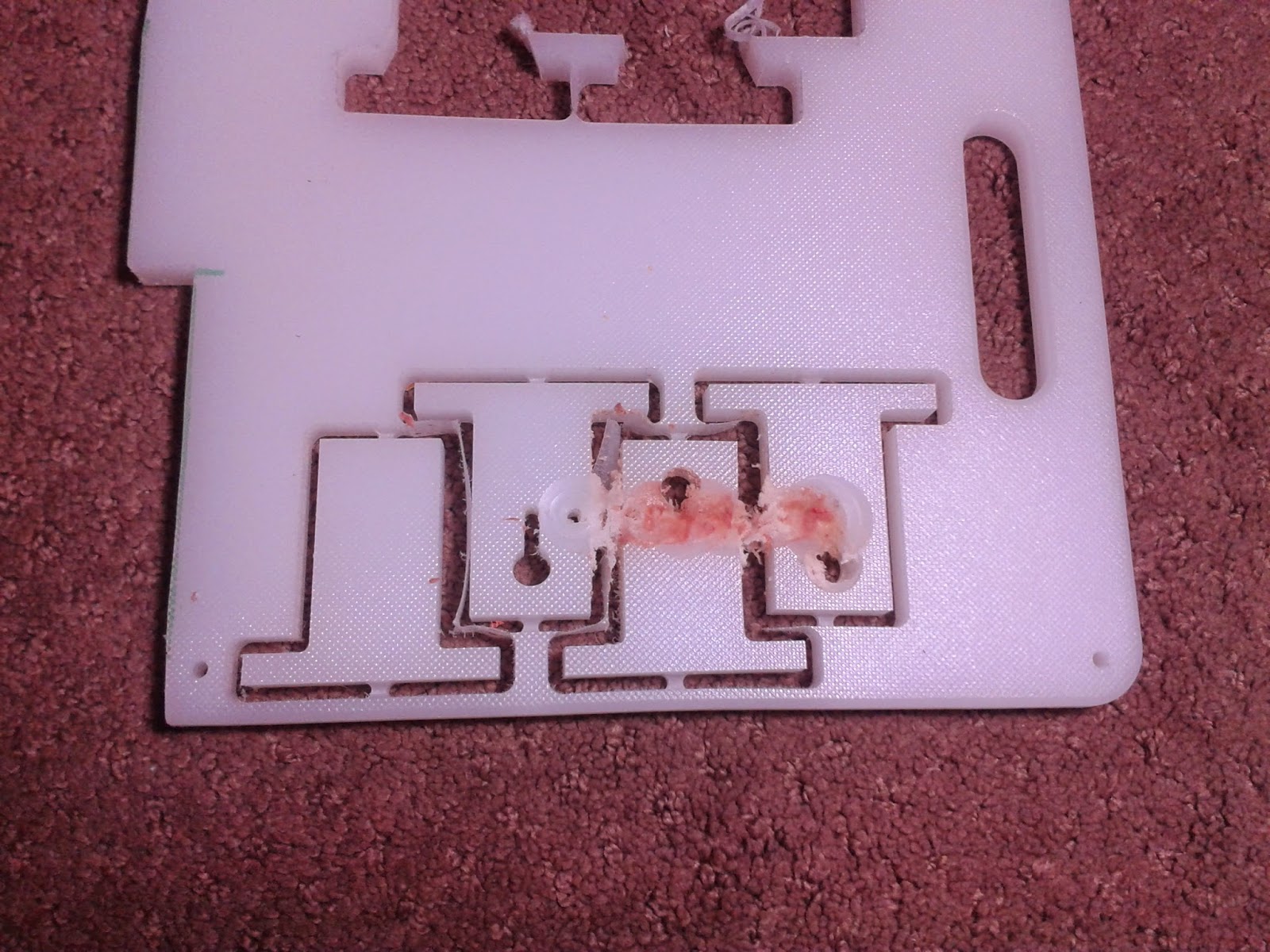 |
Brown area is where the Z-axis failed |
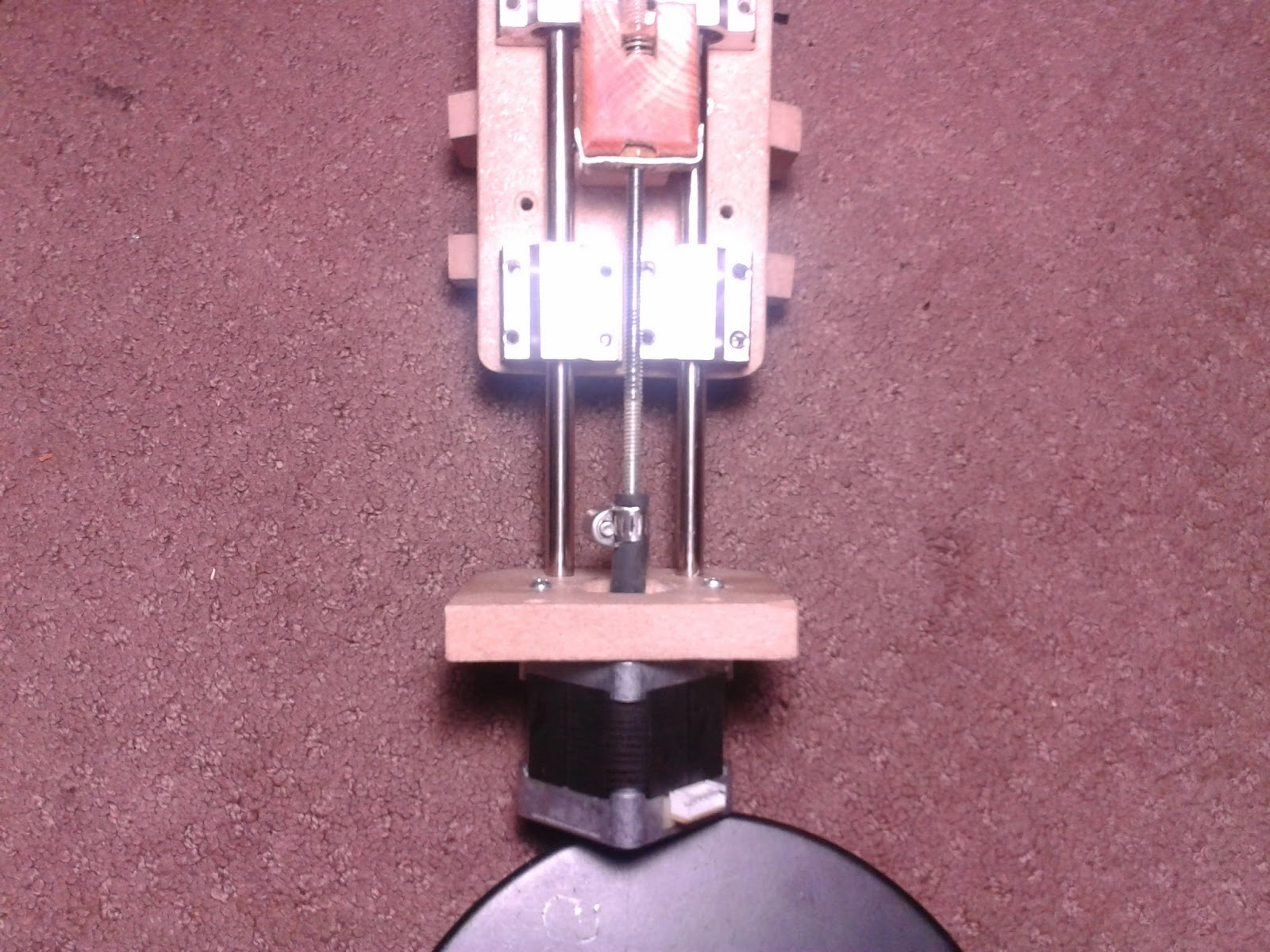 |
Between pipe clamp and motor tubing came off |
When the tubing connecting the Z-axis to the lead screw separated the spindle dropped down to its lowest limit and the X-axis continued to drag the spindle (I watched it happen and it took me a few seconds to understand what happened and shut off the power).
The parts I was cutting were supports for the Y-axis guide rods for the 3D Printer I'm building. Initially I designed and cut them out of a white HDPE (plastic) Kitchen cutting board but I did not take the stepper motor dimensions into account and they were to short.
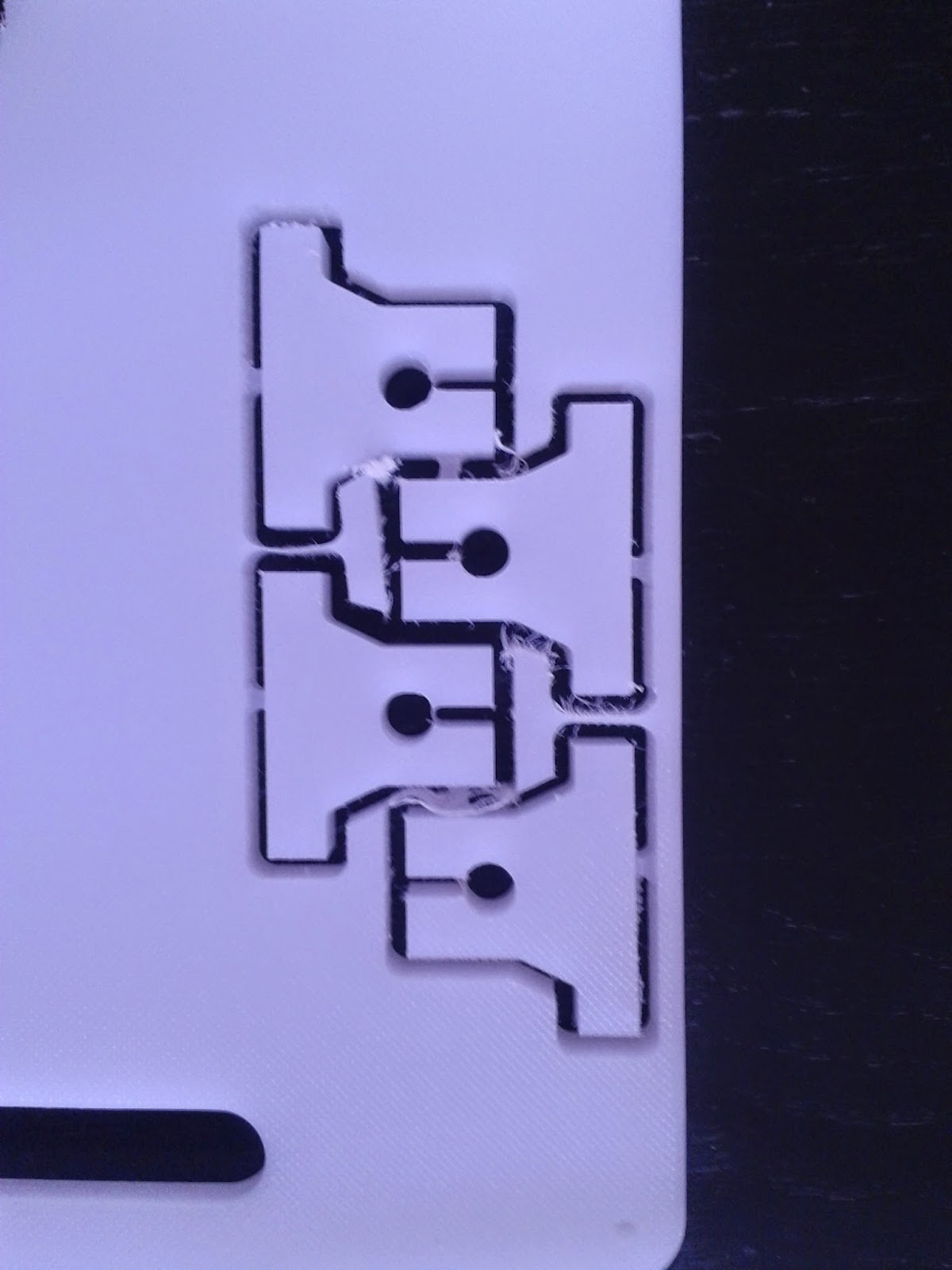 |
Initial guide rod mounts |
|
|
Mother's Day Present (still working on it...)
Prior to this equipment failure, and subsequent repair, I was able to do a bit of glass etching with my desktop cnc. My goal was to make an etched glass edge lit display/sign for my wife for her new Nut Free Bakery (
Callie's Cuties).
- I did the initial design in Inskape converting image files of the logo etc. (to keep it simple I made sure to use inches for units in Inskape - more on this in step 5). These then I resized and then used "Trace Bitmap", located under the "Path" tab. After making sure that everything was converted to a "Path" I saved the file.
- After opening a web browser window I went to MakerCAM.
- Before opening my Inkscape ".svg" file in MakerCAM I clicked in "Edit - Edit Preferences".
- In the "SVG Import Default Resolution Box" I changed it from "72" to "90"
- I then clicked on the "File - Open SVG" and selected the file I wanted on my computer (to keep it as simple and straightforward as possible keep the settings set to inch, in the upper right of the MakerCAM window - if you must use mm you will need a Python extension to truncate the measurements from Inkscape to 4 decimal places, this is automatic in inches, because GRBL cannot handle more decimal places than that).
- After my file was imported I did some additional editing (mainly cutting out unwanted parts).
- Time to select each object (left click/hold and drag) and then select "CAM - Follow Path"
- For each of these I set my depth to 0.01" with a pass depth of 0.01" and plunge and feed speeds at 14.
- After it all looks good select "Calculate All" under the "CAM" menu.
- Now it is time to export the G-Code. Select "Export G-Code" under the CAM tab and save your file.
- IMPORTANT: Open your exported file in a text editor and add "%" at the beginning and end of the file (this is not done by MakerCAM but is needed if you plan to use Universal GCode Sender)
- The bit I used was a diamond coated dremel bit for glass etching/engraving. To keep things cool I used a spray bottle filled with water and sprayed the bit as it cut.
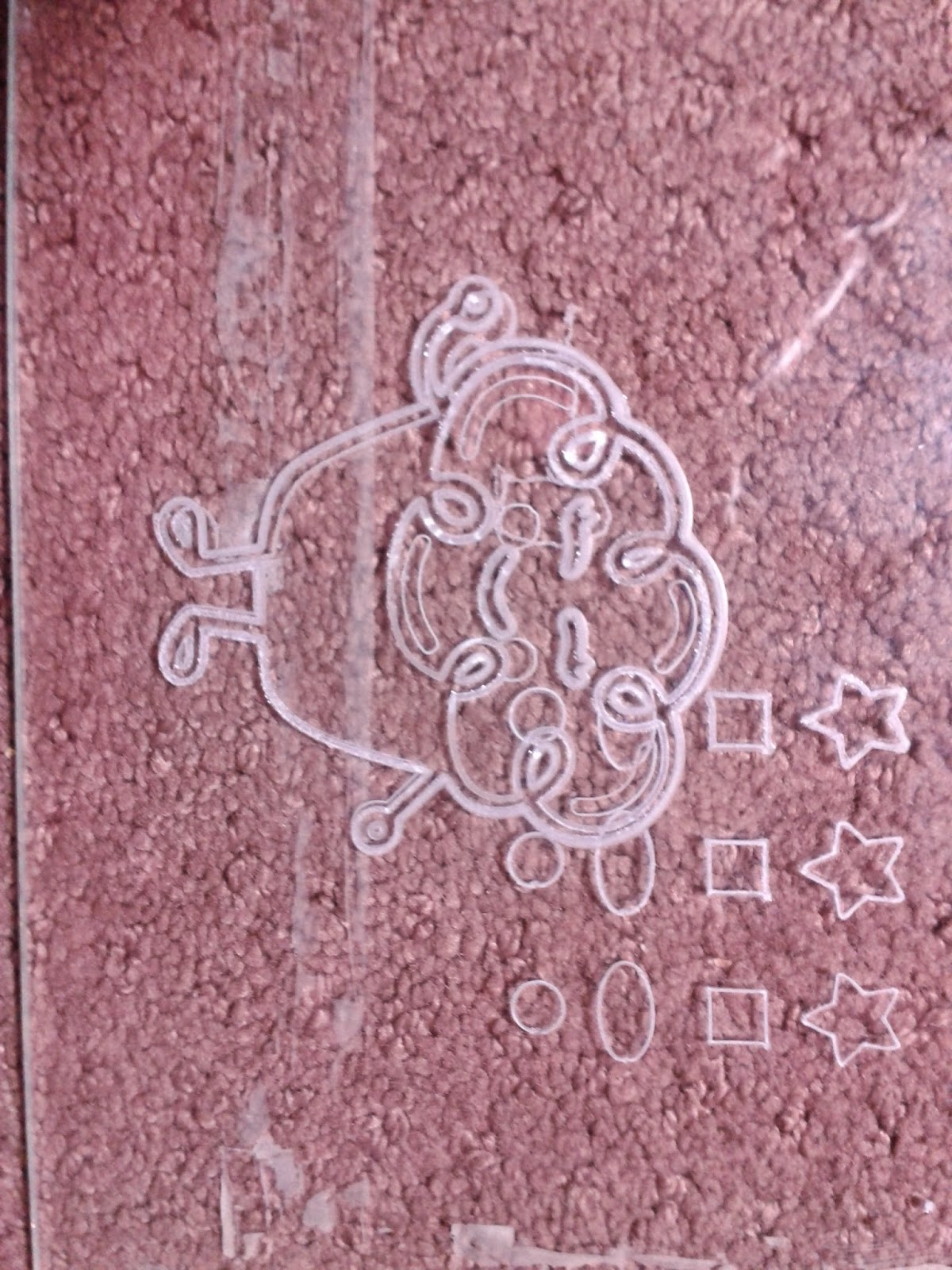 |
First test piece |
On my first test piece (above), I was checking for an optimal depth with star, square, ellipse and circles for test shapes. The bottom cut was 0.01" one pass, next up was 0.02" in two passes and finally 0.03" in three passes (each pass was 0.01" deep). In these tests I was using feed speed of 13. The Cup Cake Character was my next test (using the same piece) and this was made initially from an image imported into Inkscape. The depth was still jut 0.01" but each line was done with 10 passes, each slightly offset (Inkscape's "Trace Bitmap" has options that result in additional closely spaced lines).
After my initial tests I tried to cut my complete design:
Came out very well, a few traces in the lettering were a bit shallow. So, testing how it came out with edge lighting I found that I need to etch the image on the BACKSIDE of the glass not the front. This meant I needed to go back to the images in Inkscape, reverse/mirror them and then run them through MakerCAM again.
In an attempt to make things a little easier I tried building a clay dam around the area to be etched and filling this with water to keep the bit and the glass cool:
Below is my best run, which was messed up by my poor skill in glass cutting (I only taught myself how to cut glass last week).
After these trials I decided to revert to using Lexan to cut the display out off, instead of glass (the glass never really got bright enough and Lexan is supposed to have better light transmission).